Heat exchangers for heating
- Capacity in kW: design, calculation
- Water/water: DHW heating
- Corrosion
- Limescale deposits
- Condensing and non-condensing boilers
- Central heating, district heating, heating stations
- Solar heating
- Cogeneration (combustion engines)
SWEP heat exchangers are compact and reliable solution for steam exchanger, DHW heating, heating, biogas and district heating stations, central heating.
Performance table of SWEP water exchangers
Heat load | Exchanger type | Pressure drop |
---|---|---|
10 kW | E8THx10 ![]() | 10 kPa |
25 kW | E8THx20 ![]() | 12 kPa |
40 kW | E8THx30 ![]() | 14 kPa |
60 kW | E8THx40 ![]() | 21 kPa |
100 kW | B28Hx36 ![]() | 24 kPa |
150 kW | B28Hx56 ![]() | 22 kPa |
200 kW | B28Hx76 ![]() | 23 kPa |
300 kW | B28Hx136 ![]() | 21 kPa |
500 kW | B35TH2x100 ![]() XB52M-1-70 ![]() | 28 kPa |
(click to expand other rows) |
The performance overview for SWEP brazed heat exchangers (water/water). Inlet/outlet temperatures are 80/60 °C on primary circuit, 50/70 °C on secondary circuit. If one of the media is an antifreeze mixture (ethylene glycol), it is necessary to increase the exchanger by about 30 %.
More expensive exchangers have higher efficiency and the secondary circuit approaches the primary one better. The heat exchanger selection depends on many variables therefore, the table shows only indicative performances. For proper design please send us the key parameters for your project. We will then provide you with the optimal design as using our specialist computer program means performance can be determined accurately for different types of media, even for special or unusual applications.
Water/water: DHW heating

The wide range of sizes of SWEP heat exchangers makes it possible to find an economical choice for heating of DHW heating, drinking water and heating. The heat source is usually a boiler, heat pump, solar panel. Domestic hot water is heated in the exchanger in a flow-through manner or can be combined with a hot water tank. With instantaneous heating, the water flow can fluctuate depending on the consumption. In this case, the pressure losses must be dimensioned for peak performance. Because the greater the water flow through the exchanger, the greater are the pressure losses (losses increase with the square of the flow).
DHW flow heater
A normal shower consumes 12 to 15 l/min. of warm water. Energy-saving showers consume 6 to 8 l/min. The comfortable temperature for showering is 44 °C. This means that for a flow heater we need a boiler with an output of about 15 kW and more. The table provides an approximate overview of heat exchangers for different outputs. The heat exchangers have ISO G external thread connections.
Heat load | Exchanger type | Connections | m3/h; kPa | l/min; kPa |
---|---|---|---|---|
15 kW | E5THx14 | 4x 3/4" | 0.66; 4 | 4.8; 1 |
20 kW | E5THx20 | 4x 3/4" | 0.88; 5 | 6.4; 1 |
30 kW | E5ASHx28 | 4x 3/4" | 1.3; 5 | 9.6; 2 |
50 kW | E5THx40 | 4x 3/4" | 2.2; 10 | 16; 2 |
(click to expand other rows) |
Heat load | Exchanger type | Connections | m3/h; kPa | l/min; kPa |
---|---|---|---|---|
50 kW | E5THx30 | 4x 3/4" | 2.2; 14 | 14,5; 2 |
100 kW | B12MTx20 | 4x 5/4" | 4.5; 22 | 29; 3 |
150 kW | B12MTx30 | 4x 5/4" | 6.5; 21 | 43; 3 |
200 kW | B12MTx40 | 4x 5/4" | 8.8; 22 | 58; 4 |
300 kW | B12MTx60 | 4x 5/4" | 13; 26 | 87; 5 |
It is not recommended to heat the DHW in a plate heat exchanger to temperatures higher than 60 °C: the exchanger might then be clogged with limescale.
Charging the DHW tank
The tables show the recommended models of heat exchangers for charging DHW storage tanks. If the source temperature is high, the exchangers are often too efficient and therefore it is advisable to connect them in co-current flow (in the tables it is marked with a cross: #).
Heat load | Exchanger type | Connections | m3/h; kPa | m3/h; kPa |
---|---|---|---|---|
10 kW | E5THx14 | 4x 3/4" | 0.5; 3 | 0.8; 6 |
15 kW | E5THx20 | 4x 3/4" | 0.75; 3 | 1.1; 6 |
20 kW | E5THx20 | 4x 3/4" | 1.1; 7 | 1.6; 13 |
30 kW | E5THx30 | 4x 3/4" | 1.5; 7 | 2.2; 13 |
(click to expand other rows) |
# the heat exchanger with this mark is designed for co-current connection; heat exchanger would be too efficient when connected in countercurrent: high temperature can bring limescale deposits being built up on plates.
SWEP heat exchangers are often used to replace obsolete heat exchangers from other manufacturers. All heat exchangers are made of stainless steel (AISI 316). Also less common multi-circuit versions are available: one heat exchanger has more connections, as two smaller heat exchangers are arranged inside in series or in parallel.
Plate heat exchanger corrosion
The typical lifespan of exchangers is 8 to 12 years. If a heat exchanger starts leaking within 5 years or less, the cause is usually a corrosive medium. If the heat source is a central supply, the provider monitors the quality of the medium. In a boiler, where the circuit is closed, there's a lower likelihood of containing aggressive substances. The issue typically originates on the heated side.
A resistance table can be found using the link.
- If a visible greenish-blue tint appears on the heat exchanger's exterior, then the copper solder is corroding. Most often it is from rusty water (free iron, manganese) from outdated heating elements. Free iron in circulation forms a galvanic cell at the interface of two metals in the heat exchanger (copper and AISI 316 stainless steel). Thus, the copper solder is gradually released into the water.
- An open expansion system accelerates corrosion by oxygen penetration.
- If two different metals (e.g., copper and steel) are in contact on a pipeline, the connection creates a galvanic cell. To prevent galvanic corrosion, the connection should be made with a flat gasket. Without this, iron or another metal may be released into the system, which can subsequently cause corrosion of the copper solder.
- Distilled water (hungry water) is corrosive to copper solder.
- A special case is material fatigue caused by frequent and large temperature changes on the exchanger. An example is the flow-through heating of domestic hot water (DHW): cold water is normally allowed and is heated by a source from a hot pipe or steam pipe.
Corrosion of stainless steel AISI 304/316 is unusual, the risk occurs mainly in the presence of a large amount of chlorides (above 300 ppm). It is not visible from the outside of the exchanger.
Does corrosion also occur in other components? Are laboratory water analyzes available? If the cause is not removed, then after replacing the heat exchanger with a new one, it will also have a short service life. Measures: find the cause, replace the medium, corrosion inhibitor, magnetic filter, change to a closed expansion system. If it cannot be repaired, then choose a more durable heat exchanger: without copper solder, i.e. all stainless steel or a gasketed exchanger.
Limescale deposits
To prevent limescale build-up, it is advisable to tune the system to low temperatures, ideally close to 60 °C. Higher temperatures are associated with faster clogging of the exchanger with limescale. Lower temperatures also increase the efficiency of the system. Another possibility is to chemically treat the water, e.g. to dose polyphosphate into the circulation. It binds to calcium ions and so prevents depositing it onto plates. Polyphosphates are not suitable for drinking water though. Information how to clean heat exchanger is in the manual or on the home page.
- Let you design for higher flow and lower temperatures to transfer the same heat load.
- The higher flow rate also brings turbulent flow into the channels between the plates. This type of flow gives self-cleaning ability to the exchanger.
- It is often appropriate to design the DHW heat exchanger in cocurrent flow. A slightly larger exchanger will be needed, but the DHW won't overheat.
- Let you connect DHW inlet into the lower port of the heat exchanger. The upward flow of water reduces the clogging of channels with deposits.
SiO2 based protection to prevent limescale deposits
Sealix is a new generation of brazed plate heat exchangers that creates a barrier and keeps water running longer:
- protection of the exchanger against corrosion caused by excessive content of chlorides/fluorides in the water;
- protection of copper solder against free iron in water (e.g. rusting radiators);
- protection against limestone deposits on the exchanger plates.
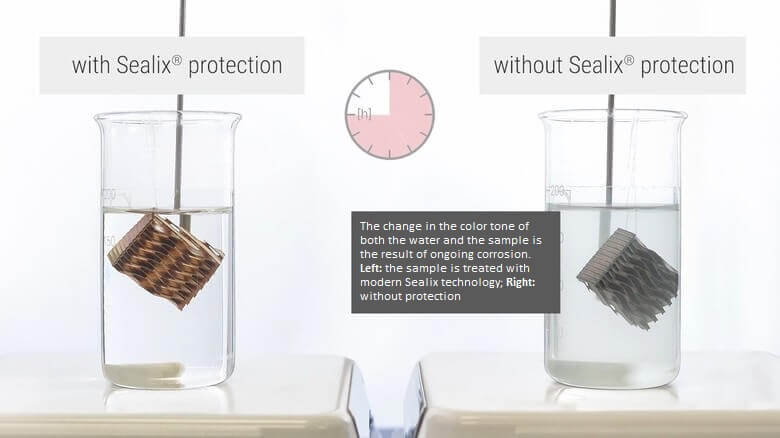
Condensing and non-condensing boilers
E5, E6, E8 series heat exchangers are designed for condensing and non-condensing boilers. They are compact and have low pressure losses. SWEP E5T, E6T and E8T heat exchangers are optimized for non-condensing boilers. SWEP E5AS, also SWEP E8AS, are often used for condensing boilers.
Central heating, district heating, heating stations
SWEP heat exchangers are used in stations for central heat supply because
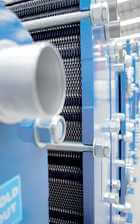
- they are compact, taking up little space in hard-to-reach areas, making their installation cheap;
- they are reliable because they undergo pressure testing before leaving production;
- in addition to the water/water system, they can also be installed as a steam exchanger;
- they do not contain gaskets and therefore require reduced maintenance costs compared to gasketed exchangers; due to the turbulent flows between the plates they have a self-cleaning ability;
- they are compact, almost every part participates in heat exchange therefore, they are extremely efficient and cost-effective.
Heat load | Exchanger type | Pressure drop |
---|---|---|
25 kW | B5THx20 | 5 kPa |
40 kW | B5THx30 | 10 kPa |
60 kW | B5THx40 | 15 kPa |
100 kW | B10THx30 | 25 kPa |
150 kW | B10THx50 | 25 kPa |
200 kW | B16Hx60 | 25 kPa |
300 kW | B16Hx100 | 25 kPa |
500 kW | B35TMx70 | 25 kPa |
(click to expand other rows) |
Biogas stations
Biogas plants produce biogas and that is used as an energy source. Biogas (its main component is methane) is produced from organic material by bacteria and other microorganisms. Biogas is burned in the engine and this is how electricity is produced. The output at one station is usually 200 to 2000 kW.
Electricity production by burning gas has a typical efficiency of 30 to 45 %. Burning gas heats up the engine which needs to be cooled, usually with water or a glycol mixture. The produced heat is removed with the help of a water-water plate heat exchanger and is also used. With such approach the overall efficiency of the system is greatly increased. The heat is used to maintain the correct temperature in the fermenter and is also used for heating, greenhouse heating, etc.
Solar heating
In the summer months, up to 1000 W/m2 can be utilized. Solar panels have an efficiency of 60 to 70 %. Under favorable conditions, the solar system can take about 500 to 600 W/m2, less in the winter months.
SWEP heat exchangers are a key component in many solar panel applications and transfer heat to water tanks, swimming pools or domestic hot water. A circulation pump is necessary to ensure operation. Larger flows increase the efficiency of the panel, but increase the pressure losses of the exchanger (more power consumption by the circulation pump). The system is filled with antifreeze solution: freezing the circulating water in the winter months would damage the solar panels and the plate heat exchanger. Ethylene glycol in concentrations of 30 to 40 is frequently used as a medium.
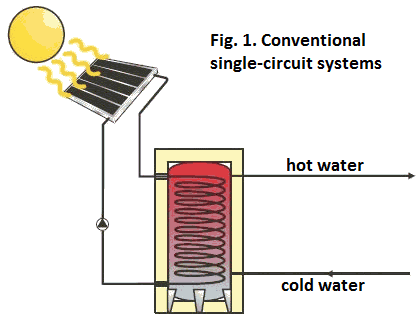

Heat transfer efficiency in conventional single-circuit systems is sometimes low. The water in the tank hardly flows, contaminants such as algae or rust on the pipes eventually lead to impaired heat transfer and poor hygiene. This leads to a further decrease in performance and raises doubts about the safety of the water in the tank. The tank needs to be opened and cleaned over time.
If a plate heat exchanger is incorporated into the system, the water in it will flow turbulently. This is the difference from a tube heat exchanger. The benefit is increased efficiency and also self-cleaning ability. The tubular heat exchanger, which takes up space, is not needed and no deposits are presented.
Because SWEP heat exchangers have a large capacity with small dimensions, they are ideal for such applications. To transfer power from solar panels, we recommend a lower series of exchangers: SWEP E8. Number of plates depends on the flow rate. The connections of these exchangers are 3/4" ISO G external thread.
Cogeneration
Internal combustion engines operate with low efficiency, often less than 40 %. Unused energy is released from the engine as heat by the exhaust. The cogeneration unit uses this waste heat, for example, to heat hot water or for heating. This is achieved by connecting a heat exchanger: this allows heat to be transferred from the primary circuit (cogeneration unit) to the secondary circuit (DHW, heating). In this way, a thermal efficiency of 80 % or more can be achieved.
Heat recovery
Industrial and commercial air conditioners operate at near atmospheric pressures, and small/compact heat exchangers are often less suitable than bulky heat exchangers that are designed specifically for such purposes. SWEP heat exchangers still have such a strong place in the industry as
- economizers,
- internal heat exchangers (IHX), or
- sub-coolers.
Pohraniční 1280/112
703 00 Ostrava-Vítkovice
Czech Republic
L | +44 74 9187 2667 |
E | +44 74 9187 2667 |
B | info@heat-exchangers.uk |
sales@heat-exchangers.uk |